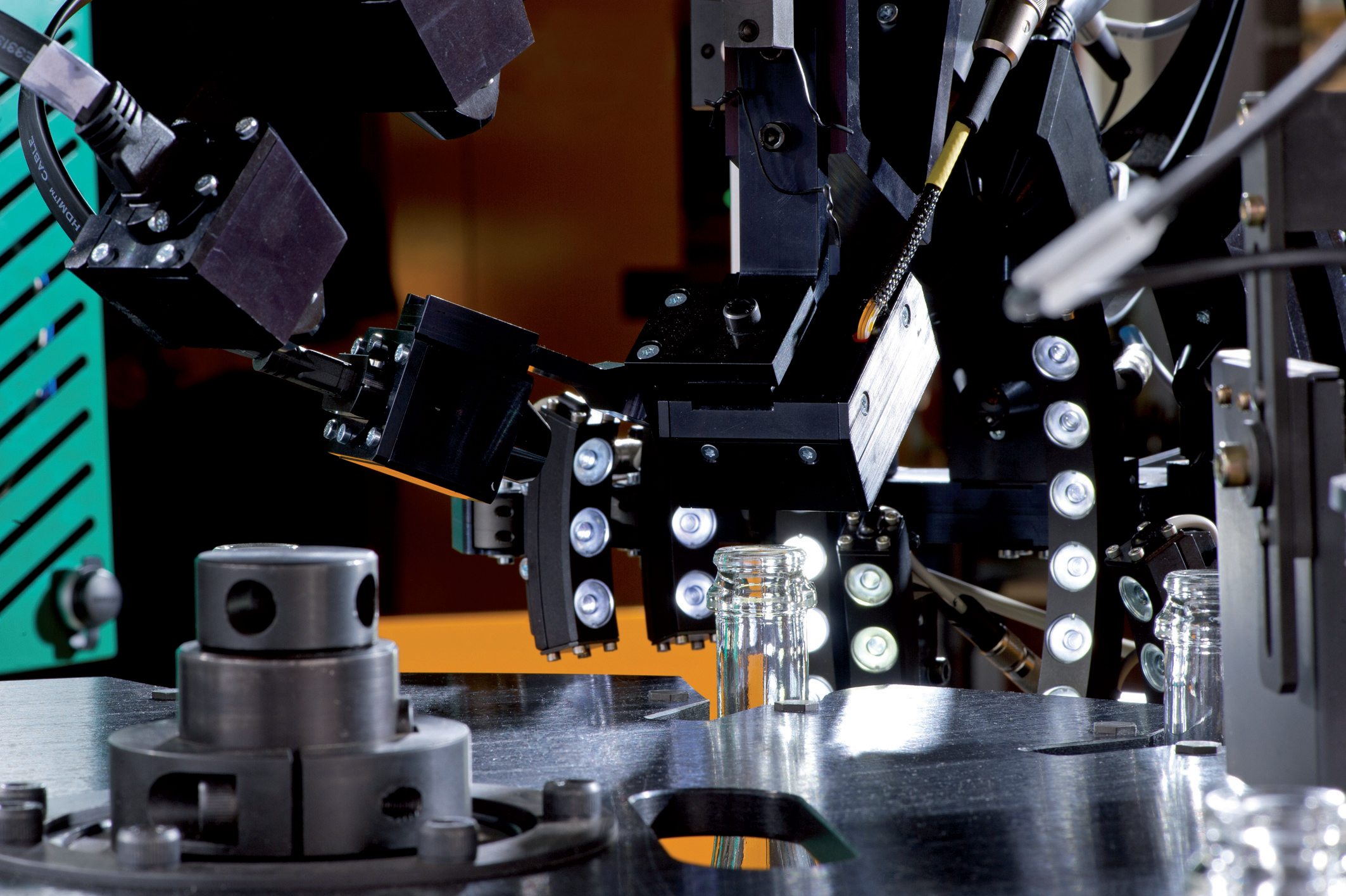
ATLAS – smart camera check detection beyond expectations
With its strong know-how acquired with our customer’s expertise and its 600 ATLAS installed in glass plants, Tiama would like to thank all its customers who participated in this success since 2006 with self-learning and automated camera check detection.
Smart modular offer based on customer real needs
The ATLAS offer is divided in 3 main modules, each dedicated to specific functions:
- Ring inspection
- Shoulder inspection
- Heel inspection
This segmentation has been thought to address real customer needs and expectations. Who could imagine inspecting only vertical cracks on a ring without ensuring a global ring control to certify that no check defect is present in this area?
However, despite this modular offer, customers, in a huge proportion, decided to purchase the full configuration including all the modules.
The 16 cameras distributed over these 3 subsets are working with 4 different modulations to strictly avoid any possible optical interference. A very easy principle to understand is that the light does not stop at the station edges. It spreads all around the light sources in any direction and reflects on all the objects in the surrounding, even stronger when most of the objects are in glass material. Therefore, even if other market players do not consider it as essential, it is an absolute necessity to synchronize the different control acquisitions with each other.
When adjusting the ATLAS, there is no need to worry about the sensor positioning depending on the other sensor adjustments but only depending on the default to detect.
Smart self-learning
No human factor is to be considered for the ATLAS setting adjustment. The inspection result does not depend on the adjuster know-how but on the machine design. The same settings quality is granted with any technician, all the time.
The ATLAS does not require any sample to be adjusted. The machine is already set to detect defects when the very first article is coming through. The settings will then continuously get improved during the learning phase and beyond. The ATLAS system only requires 500 containers to reach its maximal performances… Anyway, which glass maker pretends to sell the firsts 500 containers of a new batch to its customers? The ATLAS profits from these firsts containers traditionally sent to the cullet conveyor to auto set itself.
The other advantage of this learning process is the job change time optimization. For a new container, the job change is reduced to only 15 minutes when equivalent systems on the market require 1 hour to reach the same level of performances.
ATLAS is the only solution on the market offering such features and associated performance for a calculated payback of less than 1 year.
Smart Data
The ATLAS device has been a pioneer of the smart industry even before the concept itself existed. The dynamic masks technology and self-learning concept have been implemented in the ATLAS system in 2007 when the term of “Industrie 4.0” originated only in 2011 at the Hanover Fair.
The last release of the ATLAS software is strongly pushing in getting more embedded intelligence to assist the adjuster in its decisions. The learning process includes smart tools to automatically prevent from any potential risk of compromising the dynamic masks.
An automated virtual sample test is integrated to realize settings simulation before their application to the production.
All these tools allow Tiama to grant the ATLAS for the highest repeatability on small complex checks, decreased risks of quality complains & increased productivity.