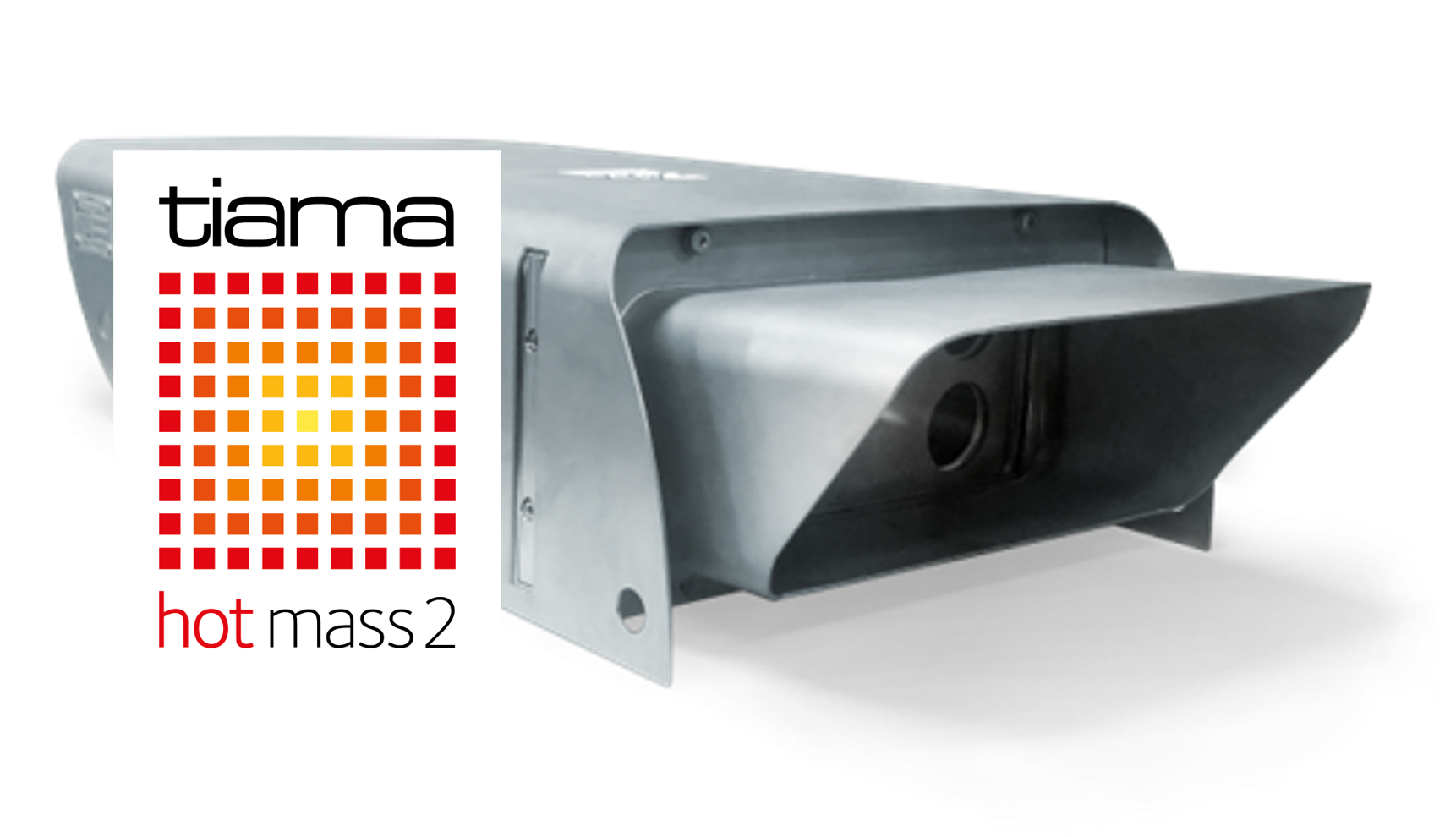
Ensure consistent product quality with early gob defects detection
Significant advancements have been made to gob monitoring systems since their introduction to address customer needs and challenges.
For instance, early systems utilized 2D gob images, while newer systems now employ 3D imaging, enabling more precise gob shape analysis for better gob weight control.
Today, environmental concerns are a major priority in the glass industry. Consequently, glassmakers are incorporating increasing amounts of cullet into their production. This cullet increase leads to less control over the glass composition, resulting in more inclusions (ceramic pieces, stones, etc.) in the glass. This trend has driven a new market demand for glass defect detection.
In response to this emerging need, a new feature has been developed on the Tiama HOT mass 2 to enable defects detection at the gob level, focusing on inclusions. The system records images of all gobs seen with defects.
The performance of the detection of inclusions in gobs is influenced by glass color. On white glass, the system can detect deeper inclusions, while on very dark glass, detection is more limited to the surface. The detection of defects at the gob level allows for initial sorting, whereas subsequent detection of inclusions on hot end or cold end machines can be more challenging, especially for items with engravings.
Furthermore, the detection of defects at the gob stage provides valuable information for process improvement. For example, detecting a high number of bubbles in the glass indicates a potential furnace temperature issue.
This new data provided by the Tiama HOT mass 2 enriches information on the process and contributes to the process optimization.
*This feature can be installed on all existing Tiama HOT mass 2 units and does not require any hardware modifications. It will be available by the end of 2024.
Defects detected with the Tiama HOT mass 2